Whether you are responsible for maintaining a Guyson wheel blasting machine or just getting familiar with wheel-blast technology, it will be helpful to know the parts of the Guyson blast wheel, the function of each component and how our blastwheel works.
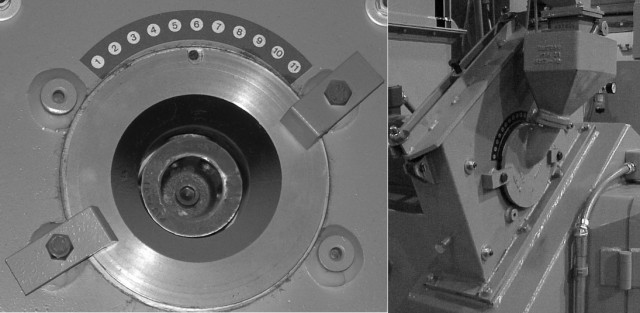
Entire blastwheel assembly with funnel and feedpipe at right, core only at left
All parts of the blast wheel assembly that are in direct contact with the shot or grit are cast from an extremely hard and brittle iron alloy that resists gradual abrasion by the effects of friction. A typical flow rate of the media through the blastwheel is approximately 150 pounds per minute, so these are very hard-working parts of the wheel-blast machine.
Metallic media is gravity-fed to the blast wheel by the adjustable feed gate, a funnel and feed pipe, where the bead flows into the core of the blast wheel or blast turbine.
At the center of the wheel is a cup-shaped component with fins called the distributor that rotates at the speed of the blast turbine and pushes the media into the blades of the wheel. This critical part shovels as much bead into the blast wheel as it can throw onto the work.
Around the distributor is the cone-shaped regulator, which is stationary and has an opening in the neck of the part that is directly surrounding the spinning distributor. This component serves to direct the flow of media into the wheel at the correct point in its rotation to make sure the bead is projected out of the blast wheel in the right pattern to cover the work and get the blasting done as efficiently as possible.
Another way to understand the importance of the regulator is to consider the centrifugal forces generated by the blast wheel as it accelerates the bead. Media flows along the blades of the blastwheel to the blade tips, where it slings out at maximum velocity. If media enters the wheel “earlier” or “later’ in the rotation of the wheel, it will gain the same acceleration and exit velocity, but it will fly out of the perimeter of the wheel on a different trajectory.
The regulator makes adjustment of the blast pattern possible. A notch in the outer rim of the regulator is aligned with one of the series of numbered holes in the blast wheel housing and held in that position by a set screw. Turning the regulator to a lower number changes the location of the window through which bead is injected into the blast wheel blades, effectively shifting the blast pattern slightly. A separate post to this blog will explain the procedure for blast pattern testing and adjustment.
Lining the blast wheel housing are armor plates fitted around the blastwheel itself. The directional armor not only protects the housing from abrasion by contact with media, it helps concentrate and direct the media streaming out of the wheel.
It is important to monitor the condition all parts of the blast wheel on a regular basis, as recommended in your machine owner manual. By noting the number of blast hours and performing inspections of the blast wheel on schedule, you can detect wear of the blastwheel blades, the directional armor, the distributor and the regulator and replace worn parts when they start to cause a decline in the performance of the wheel.
Blast wheel inspection procedures are described in your owner manual. Also, a maintenance bulletin dedicated to the subject is available from the Guyson Customer Service team. To ask a question about the performance of your Guyson wheel-blast machine, discuss blast wheel maintenance or get a quote on spare parts, contact us by calling on our toll-free Customer Service Hotline from anywhere in the U.S.A. or Canada at 1-800-633-6677, or send an e-mail to custsvc@guyson.com.