Prepping metal to achieve a perfect anodized finish can be a complex process. Whether you are working with aluminum, magnesium, titanium or zinc, the metal first needs to be prepared the correct way to achieve the best results. The strongest, most resilient, hard coat finish is a Type III Anodize finish, which is achieved through an electrochemical process that converts the outer surface of the metal into a protective, colorized, corrosion resistant anodic oxide finish.
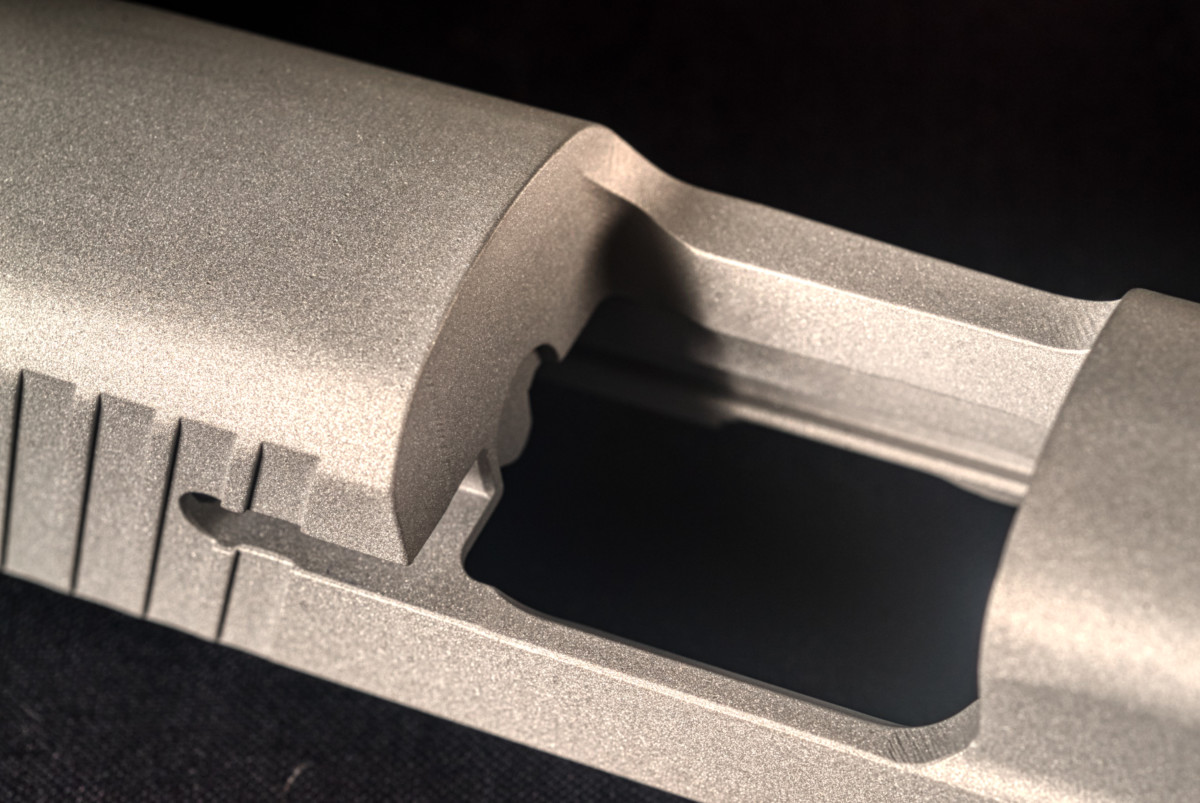
Guyson Corporation, a leader in the metal finishing industry, has done extensive research into prepping aluminum for an anodized finish. The company has created a series of machines and media that are specifically tuned to produce the best anodized finish.
Getting the right Type III finish is an exacting process that results in a harder, more corrosion-resistant coating. Guyson has done extensive research on how to achieve the proper finish for anodized aluminum parts through its extensive work with the firearms industry. Our machines have earned a stellar reputation for delivering consistent and repeatable finishes at high volumes.
Although an oxide finish provides resistance against the elements, the cosmetic look and texture of a part is created in the finishing process. Over-blasting can create microscopic spikes in the aluminum which can break off after the anodization process. This exposes the original metal to the environment and changes the color of the anodized product. A flat black finish will turn to a flat grey in areas that are in use most often.
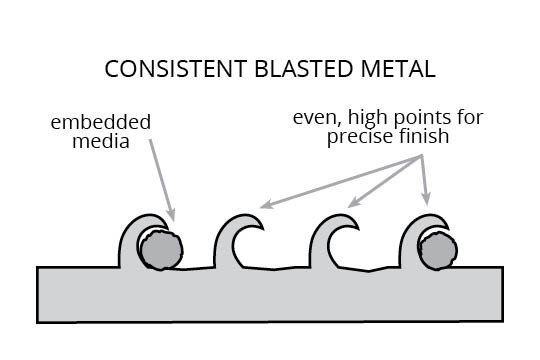
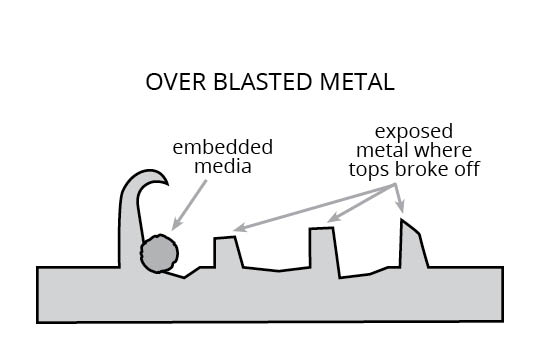
MIL-A-8625F, Military Specification: Anodic Coatings for Aluminum and Aluminum Alloys
The most precise anodized specification is MIL-A-8625 for the military and aerospace industries. This is the specific STANDARD for many components. This specification covers all the requirements needed for six types and two classes of electrolytically formed anodic coatings on aluminum and aluminum alloys. Guyson’s machines are designed to prepare aluminum parts for MIL-A-8625 specification.
Guyson’s machines built specifically to prepare aluminum for an anodized finish
1) Wheelblast cabinet
Our 401T AR-MAX and the 402T AR-MAX 2T, are high volume, low cost units that have small footprints and consume less air pressure. We have created special blast media that our research shows exceeds the manufacturer specifications for a superior anodized finish.
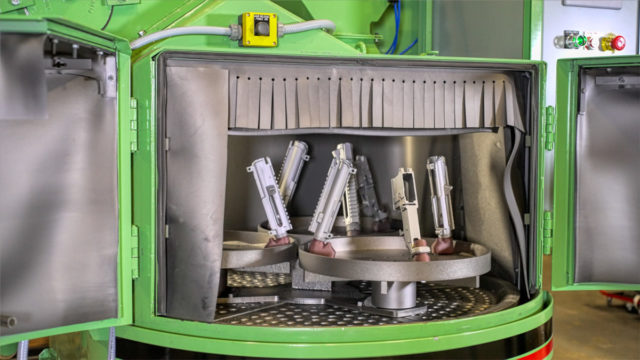
2) Guyson RXS systems
A rotating Indexing blast cabinet (Guyson RXS systems) is an automated machine that has an exact and repeatable process enabling the machine to get a consistent finish on every product. Guyson makes cabinets of multiple size and accessories making this machine one of the most productive in the metal finishing industry.
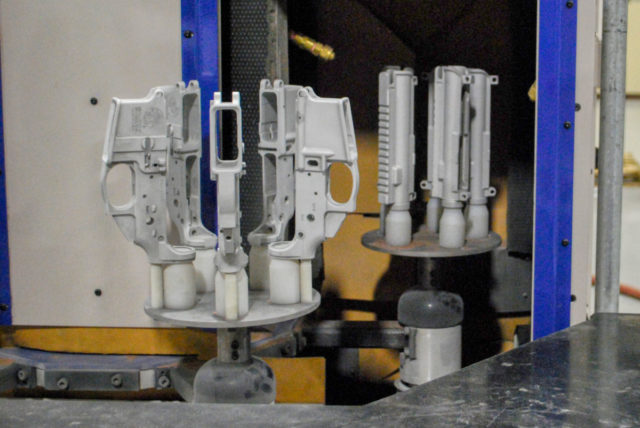
3) Rotating Indexing Blast Cabinet (using wetblast media)
Our wetblast cabinets can be used to create more of sheen to your product. Because the wet blast process does not embed media in the metal, it still creates a roughened surface, but with a more polished look. This can also be built with the same enhanced production features as the Guyson RXS dry blast systems.
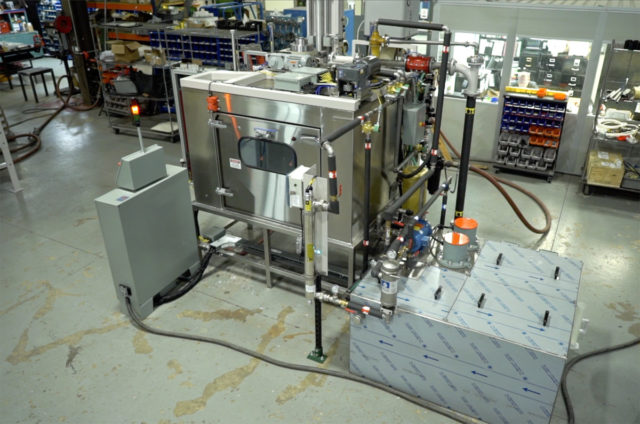
4) Tumble Blast Cabinet
Tumble Blast Cabinet – for small parts, like triggers, and other accessories
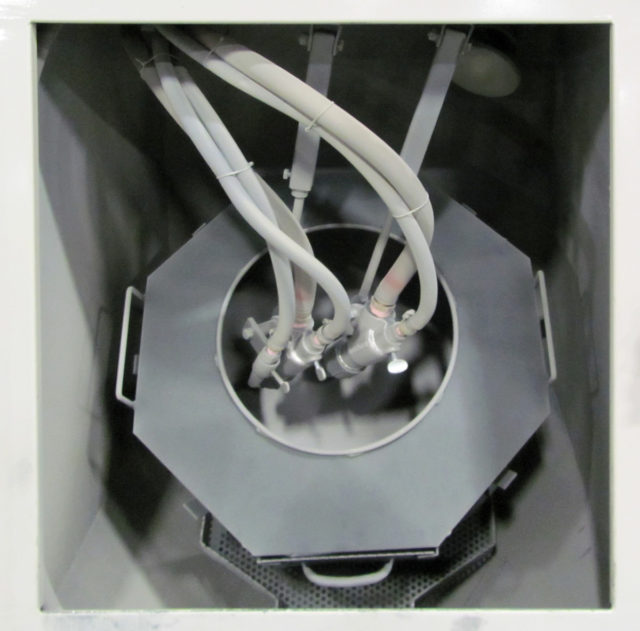